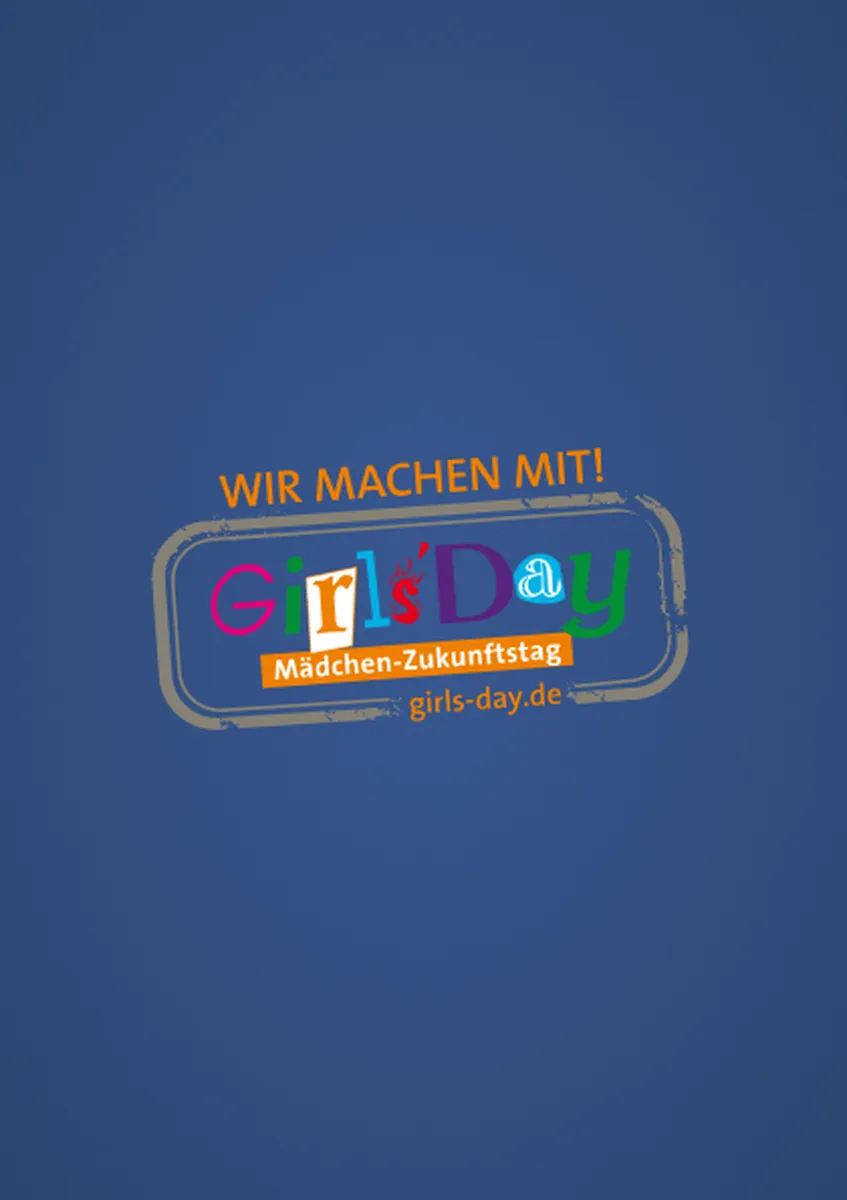
Production in Synchronization: Integrated Solution with Automated Assembly and Cohesive Test System
Konrad Technologies is setting new standards in the dynamic world of custom machine construction with its pioneering solution: "Production in harmony". This innovative approach combines automated assembly and an integrated testing system to create a seamless process chain. Konrad Technologies is a pioneer in the fusion of precision and quality to create top products in custom machine construction.
Comprehensive customer services in all areas
Konrad Technologies has expertise in system construction as well as in test systems and automation. The customer has a single point of contact for all matters. This minimises the costs of commissioning and installation times at the customer's premises. With its own international locations, Konrad Technologies is able to plan, build and support systems worldwide.
The latest production line, which has been tailored to individual customer requirements, has been delivered to the customer in March 2024 following a successful overall preliminary acceptance test (FAT).
Manual loading with digital monitoring
The manual loading of the individual components at the first station of the production line is already digitally controlled. An advanced camera system ensures seamless verification that all components have been inserted correctly. The reading of DMC codes enables smooth synchronisation with the customer database.
Automated assembly with real-time quality control
At the next station, a special compounding is applied automatically and checked for quality using high-resolution cameras. At the same time, the test specimen is carefully and automatically assembled while accuracy and conformity are monitored. This innovative combination of automatic assembly and real-time quality control ensures that every test specimen fulfils the highest standards of precision and reliability.
In station 3, the test specimen is precisely screwed together in a fully assembled state to ensure a stable and reliable unit.
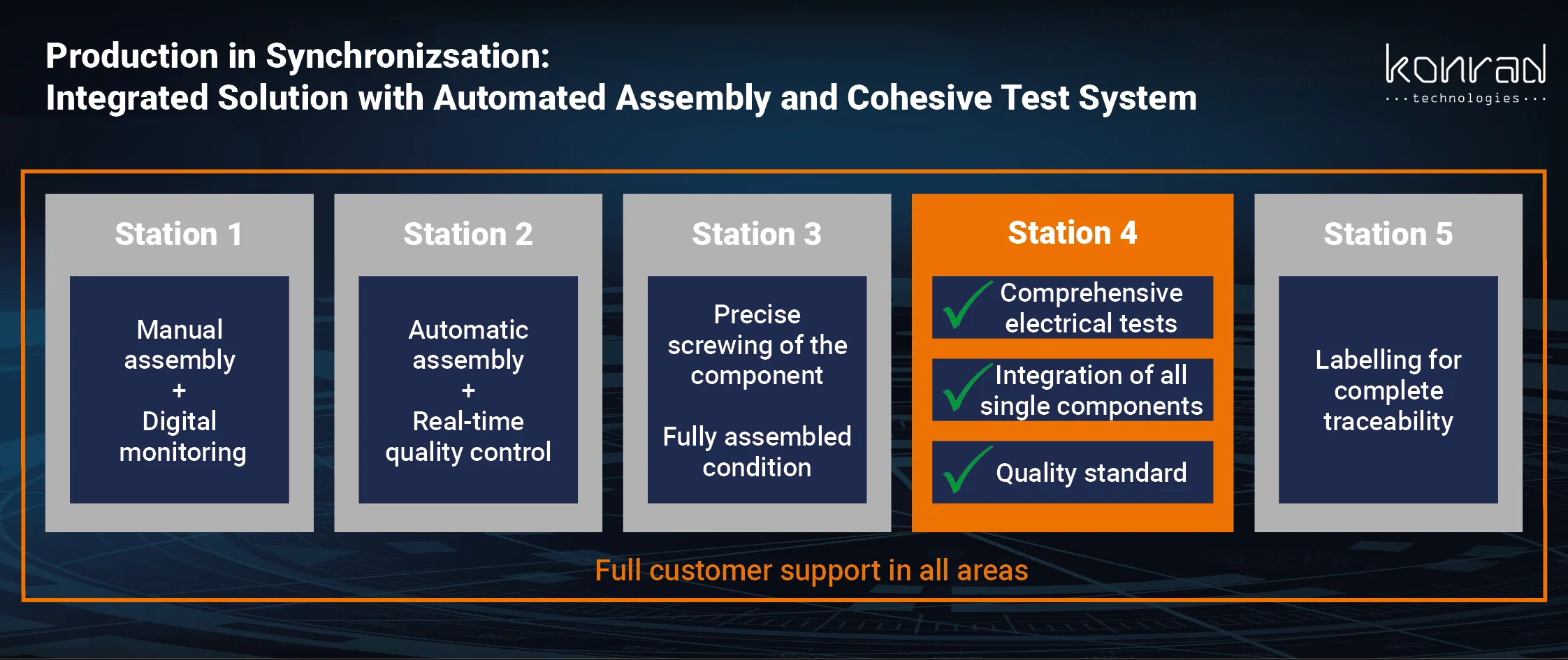
In-depth electrical testing guarantees the highest quality
At the crucial station 4 of the production line, a thorough electrical test forms the basis for the highest quality. This station is characterised by a comprehensive test that ensures the seamless integration of the individual components previously identified in station 1 into the test specimen.
Labelling for complete traceability
Finally, a label is printed on the test specimen in the fifth station. This label is not only used for labelling,but also enables complete traceability throughout the entire product lifecycle.
The careful combination of these test procedures and programming steps in station 4 emphasises the commitment to the highest quality standards and innovative technologies in custom machine construction. The result is not just a product, but the highest level of precision and reliability for the most demanding applications.